
电动汽车是采用动力电池供电,以驱动电机运转,从而驱动整车前行的汽车。区别于传统车,新能源汽车的核心技术是“三电”,包括电池、电控、电驱动。
电池
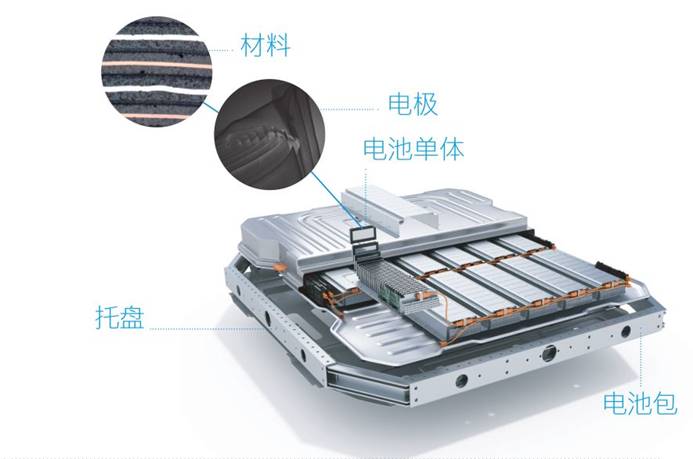
电池会影响电动汽车的性能、行驶里程和寿命。无论现在还是将来,安全性、使用寿命、 性能和成本都是决定电池技术成功发展的关键因素。在电池的设计、研发、质量控制和生产阶段需要将这些因素考虑在内。因此,必须从材料、电池单体、封装、托盘以及各种(特征)精度级别上了解和控制电池性能。在组装电池组和托盘时,需要满足耐潮标准,这对汽车的安全性非常重要。
1为了生产高效可靠的电池,必须严格控制原材料的质量(阳极和阴极材料、隔膜、铝箔或铜箔),并且要确保生产的电池不会出现诸如颗粒污染、叠片不齐或电解质填充困难等问题。此外,还需要不断研究新材料,例如通过降低钴含量来降低成本,或通过改善充放电循环(效率)来提高性能;了解锂离子电池的老化效应,可以延长电池的使用寿命,从而提高客户满意度。
2为了对电池进行研究和质量控制,需要利用大量的成像、分析和计量工具。保定蔡司的保定光学显微镜、电子显微镜、保定X射线显微镜、计算机断层扫描(CT)系统和保定三坐标测量机可以用于在不同的尺寸精度下评估以及关联电池的结构、成分、电学性能和尺寸信息。蔡司通过提供这些相关数据,帮助进一步提高新能源汽车的电池安全性和性能。
电控
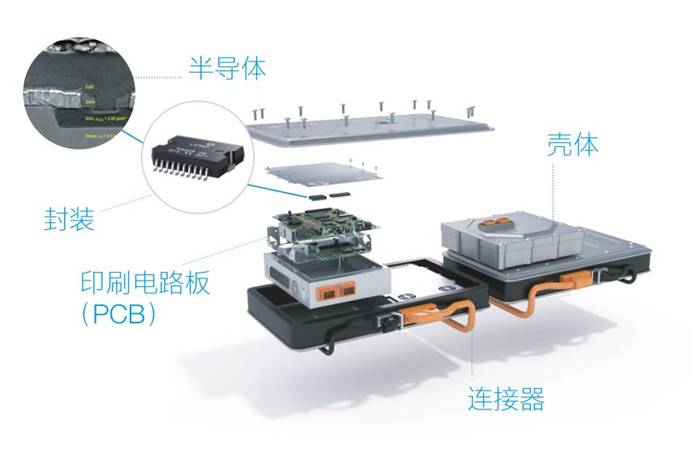
因为电控单元控制着电池和电动机之间的能量流动,因此它是每一辆电池动力汽车的能源中心。为了让电子元件更加高效和可靠,对于不同精度级别的半导体器件、封装件、印刷电路板(PCB)、连接器和成品模块的质量控制非常重要。
面对轻量化和适应严苛工作环境的大趋势,电子元件日益呈现高度集成化和微型化的特点,但同时又不能降低其可靠性,因此对质量控制的要求也越来越严格。此外,失效分析也成为了一项颇具挑战性的任务,因为问题的根本原因可能存在于任何涉及的组件中。
对于一般的质量控制工作,可以采用各种光学和接触式设备进行光学检查以及关键尺寸和/或表面粗糙度的检测。此外,无损X射线解决方案可用于壳体、连接器的质量控制,X射线显微镜解决方案还可用于更高精度要求的PCB和半导体封装的检测。最后很重要的一点,失效分析工作流程需要成像和分析工具能够覆盖从毫米到纳米不同精度级别的表征,而蔡司的Connect解决方案(包括X射线显微镜、光学显微镜和电子显微镜解决方案)通过对所有结果的关联提高了生产率。
电机
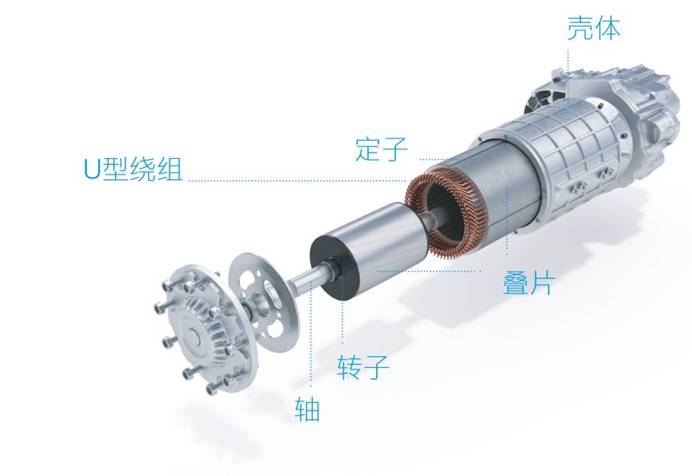
电动机小巧轻便,它是真正的动力源,即使是在低速下行驶仍能保持高转速和大扭矩。所有组件都需要精确地安装在一起,以便电机在低磨损的情况下能够产生大功率。最新一代电动机所带来的挑战涉及U型绕组的精确生产,以及定子和转子所用叠片的制造和装配。
紧凑型高性能电机中的许多组件均采用自动化生产流程。例如,定子内的绕组线圈不再是由许多细导线缠绕而成,而是由实心铜线弯曲,插在一起焊接而成。虽然这种弯曲动作完全采用自动化,但由于销的柔性结构,对测量销形状和绝缘层厚度仍提出了质量保证的挑战。这些U型绕组最终需要装入精确的压线冲子或切入定子叠片中。这种高精度的装配工艺需要精确到毫米级,而这正是蔡司的优势所在。
蔡司可以为高效、可靠且耐用的电机提供接触式和不同的光学测量设备,比如2D相机、激光三角法测量和共聚焦白光传感器,能够涵盖质量管理流程的各个方面。从手持激光扫描仪到高精度的三坐标测量机,这些设备在整个生产过程中的多个环节都能用于基本的质量控制,无论是从原型阶段到装配线,还是在二维或三维空间中。作为精密工程领域的专家,蔡司还可以为每个制造商设计和建立理想的检测链。
传动
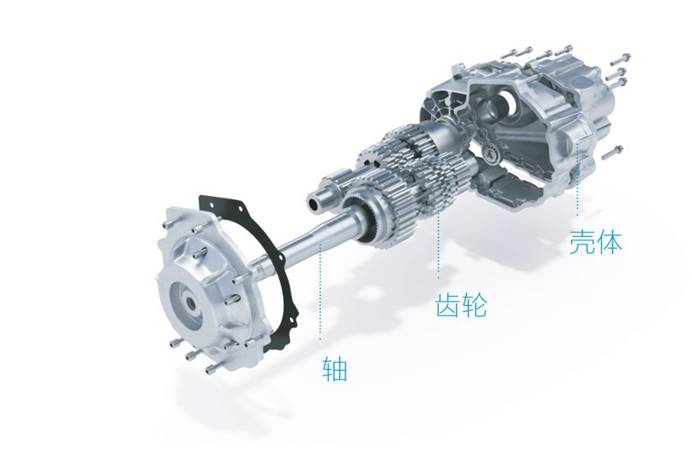
电动汽车拥有和传统汽车完全不同的动力系统,仅用2个挡位便替代了之前的9个挡位。在电动汽车中,电动机和变速器共用一个外壳,在不降低质量的情况下,减少了部件的数量和重量。许多测量和检查步骤需要互相关联,以便确保拥有最高性能、最低磨损和最安静的操作。
如果发动机的转速高达20000rpm,那么变速器的齿轮必须满足非常小的几何公差。转速对转子和齿轮轴的形状和位置公差要求也很高,特别是轴承和齿轮所在的位置。将电动机和变速器放在同一外壳内需要采用非常复杂且轻便的设计,包括在铸造的外壳上进行精密加工。这些部件的形状、尺寸、位置或表面质地的微小偏差都会影响动力系统的功能和安全性。蔡司拥有进行此类精密检测所需的所有测量工具。
计算机断层扫描(CT)可以对变速器外壳铸造内部材料的缺陷情况进行无损检测。高精度三坐标测量机拥有测量尺寸、形状和位置公差的传感器,以及用于测量表面质量的粗糙度传感器,可以对其余传动部件进行精确测量。除了不断研发具有突破性的测量技术外,蔡司还会继续提供相关建议和支持,以确保客户能在自己的生产设施中充分利用这些设备。